
TASK RIGHT SOLUTIONS
COMPLETE CARE MAINTENANCE SERVICES
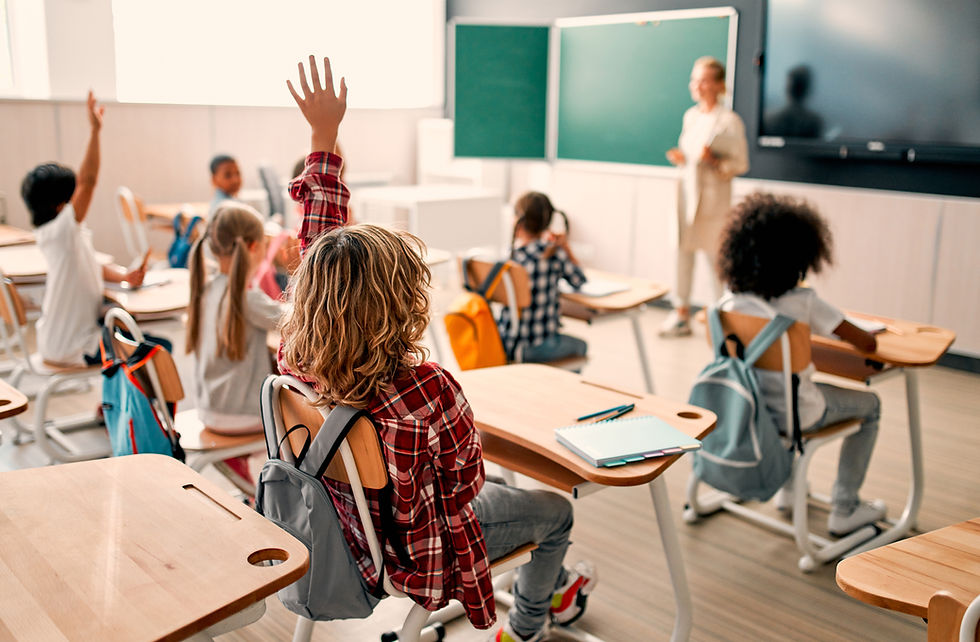
FAQs Frequently Asked Questions
Why do we need maintenance?
Maintenance combines proactive and reactive actions to keep machinery, facilities, and equipment running efficiently and safely.
Different types of maintenance, like planned, reactive & preventive, including condition-based, each address specific needs and help prevent costly breakdowns.
What is planned maintenance?
Planned maintenance is a strategy that allows facilities teams to proactively manage assets and facilities. Encompassing both preventive and corrective maintenance, planned maintenance helps to reduce reliance on costly reactive maintenance.
Planned maintenance is often required to obtain permissions to operate, specifically where it relates to critical systems. For example, buildings must have an operational fire safety system before any kind of occupancy is permitted. The regular inspections of, and maintenance on these systems forms a part of planned maintenance strategy.
Part of the compliance obligations surrounding these systems is being able to prove that the work was conducted, and report on that work in a reasonable timeframe.
​
Why reduce reliance on reactive maintenance?
Reactive maintenance is an essential part of maintenance strategy. However, over-reliance on reactive maintenance creates unnecessary costs and inefficiencies.
When it comes to critical systems, relying on reactive maintenance exposes the business to significant risk. If a critical system is to fail, the business has to stop operations until the issue is resolved.
By implementing a planned maintenance strategy, the risk of a critical system failing is significantly reduced.
Additionally, often the organisation has to prove that planned maintenance has been conducted, as a condition to attaining permissions to operate.
What is preventive maintenance?
Preventive maintenance is a core part of planned maintenance, and refers to work and inspections done on a regular schedule. The difference between preventive, and corrective maintenance, is that corrective maintenance is done in response to a maintenance need uncovered during the course of these regular inspections.
For example, preventive maintenance would be a regular inspection on a fire sprinkler system. Corrective maintenance would occur if during that inspection, a non-urgent maintenance requirement was uncovered, for example a loose washer.
If that washer had degraded and caused a noticeable leak, fixing it would be considered reactive maintenance.
​
Is there a need to test and tag?
Test and tag is a crucial component of workplace health and safety, and failure to comply with regulations can result in fines, legal action, and even workplace accidents.
How often dose testing and tagging need to be done?
3 months: Building, construction and demolition - this requires the most frequent testing due to it being considered a harsh environment and therefore an appliance being damaged is more likely compared to other settings.
6 months: Factories, warehouses and production - this type of an environment isn't considered as harsh, but because appliances are often used constantly it needs to be tested every 6 months.
12 months: An environment where the equipment/supply cord is prone to flexing or open to abuse - this is often referred to as a hostile environment as the appliance can be overused and is therefore exposed to abuse by the user, as well as dust, general deterioration and the weather.
5 yearly: An environment where the equipment/supply cord is not prone to flexing or open to abuse - this is commonly referred to as a non-hostile environment - a typical example of this might be a company's server room.
​
What jobs are included in commercial gardening?
A lot of the jobs associated with domestic gardening that you may be familiar with are also carried out with commercial gardening but on a much larger scale.
These jobs include:
-
Jet washing - Jet washing is an effective way of cleaning patio areas, car parks and paths. It will remove any dirt and grime that has built up. Paths and communal seating areas are important spaces for any commercial and communal area so it is vital to keep them clear and clean.
-
Hedge care - Regularly pruned hedges give a professional look and ensure that the outdoor space does not get overgrown.
-
Lawn mowing - A well-maintained lawn is crucial, not just for aesthetic reasons but for practical purposes too. Often a large grassy area may be used for a children’s play area so it is important to keep this clear. An overgrown lawn can also often be a very large space so it is much more pleasing to the eye to be kept short and well-kept. Sit-on lawnmowers are often used to mow large lawns quickly and efficiently.
-
Weeding and general plant care - Well-maintained beds are critical to the longevity of a commercial area. Bushes and plants will be positioned with future growth in mind to give the desired appearance over the coming years as those plants become established.
-
Litter picking - Whilst this is not the typical role of a commercial gardener, any litter in commercial areas will be removed to keep the communal spaces clean and tidy.
-
Leaf clearance - Falling leaves may look pretty but once on the ground, leaves can become a slip hazard. Any fallen leaves will be removed from areas of high footfall to prevent the risk of slipping.
-
Watering - Shrubs and bushes will be watered at every visit and it is ensured that all plants provided will be low maintenance and easy to care for.
​​​​
Are your cleaning products safe?
Yes, we use environmentally friendly, nontoxic cleaning products. This ensures the safety of our clients, their families and the environment.